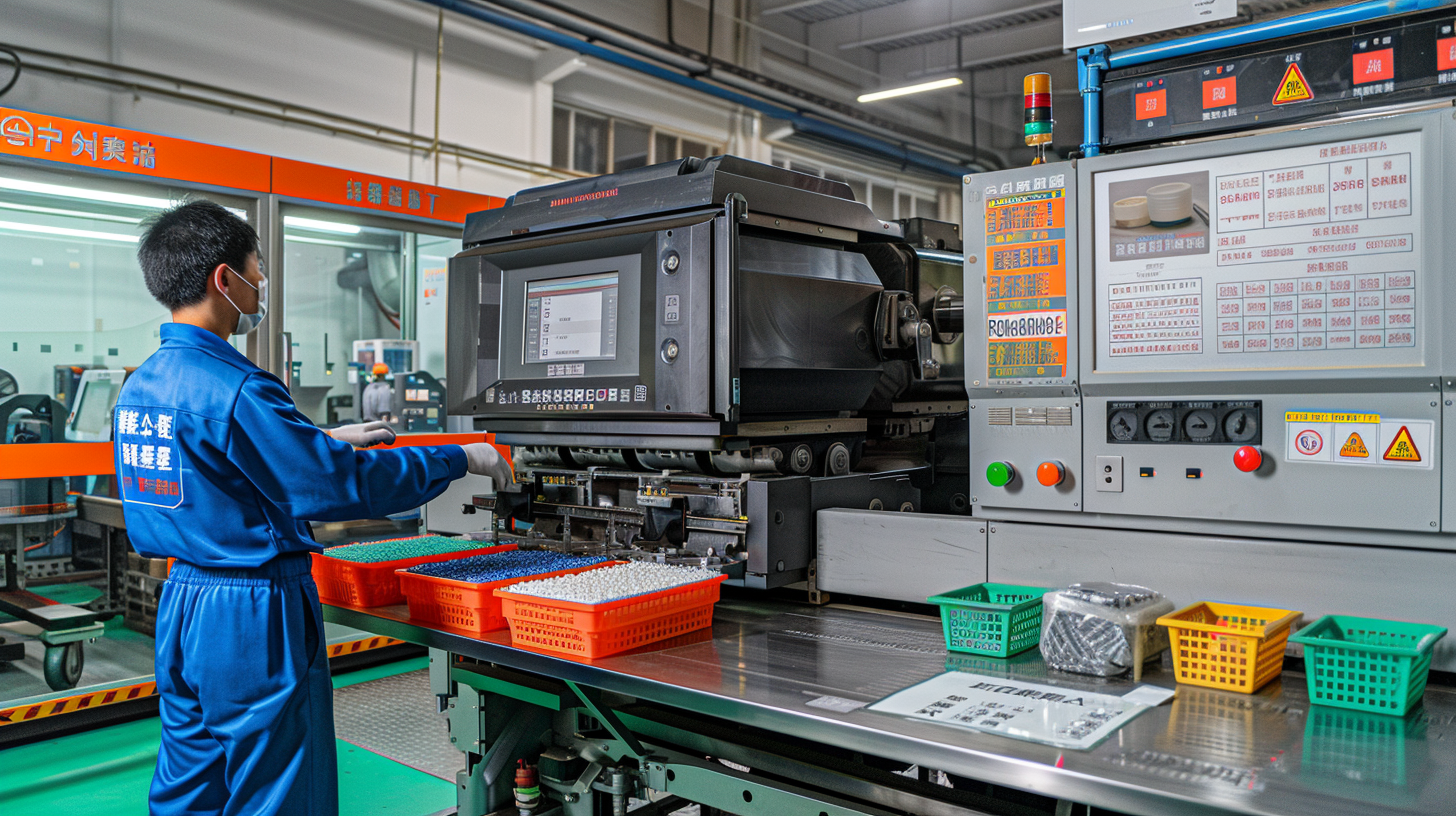
Minimizing material waste in injection molding not only improves sustainability but also cuts down on production costs and increases efficiency. The best ways to reduce material waste include optimizing mold design, improving material usage, controlling process parameters, and implementing recycling strategies. These approaches help manufacturers produce high-quality parts while minimizing excess plastic waste.
Let’s explore the most effective ways to reduce material waste in injection molding.
How Does Optimized Mold Design Reduce Waste?
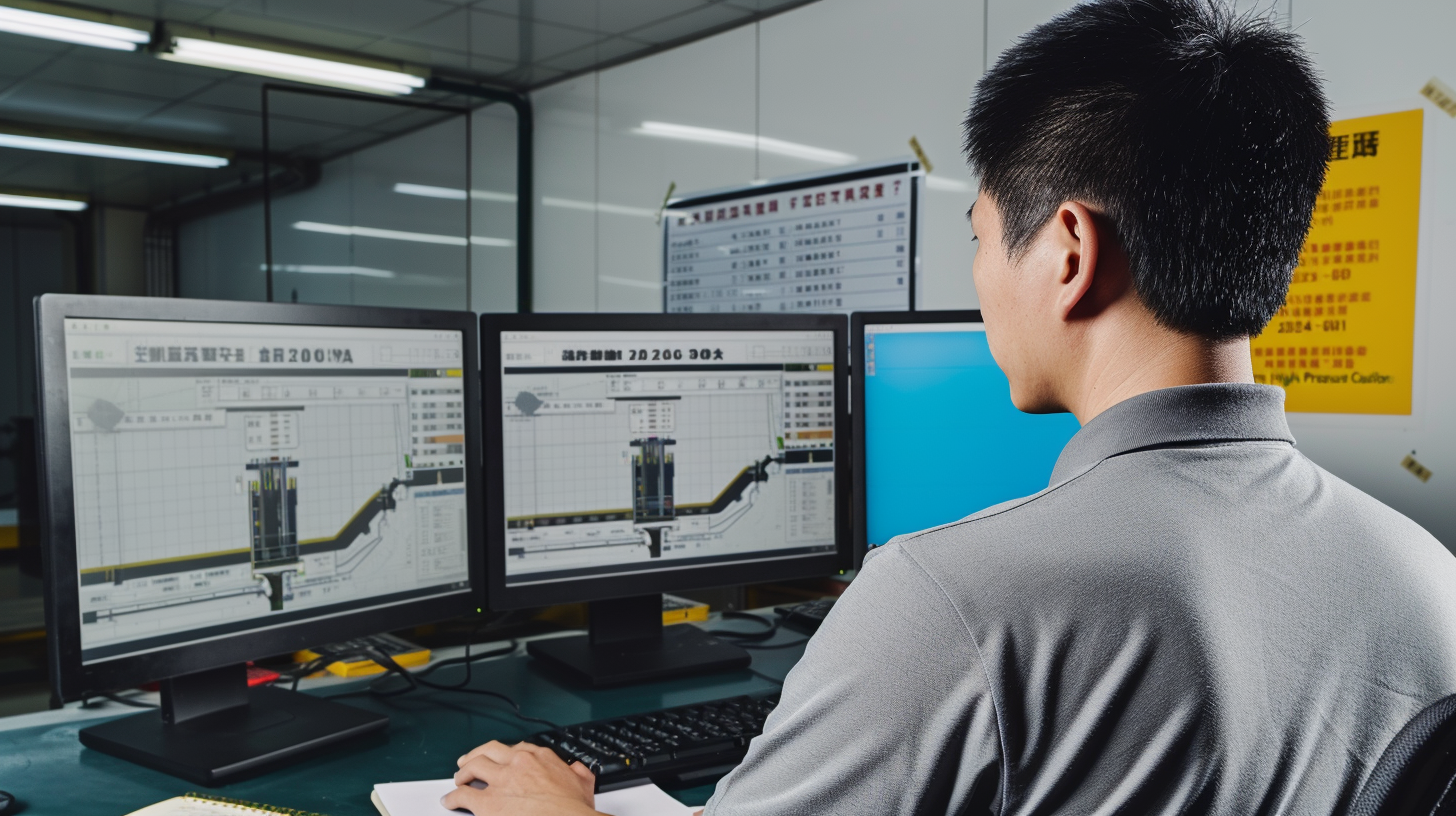
Well-designed molds prevent excessive material use by ensuring proper flow, minimal scrap, and efficient cooling. Poorly designed molds can cause defects like flash, short shots, or excessive sprues and runners, which contribute to waste.
Best practices for mold design to minimize waste:
Use Hot Runners: Unlike cold runners, which generate waste after each cycle, hot runners reduce material waste by keeping plastic molten for reuse.
Optimize Gate and Runner Placement: Properly designed runners minimize unnecessary material flow, reducing scrap.
Minimize Overpacking: Excessive pressure in the mold can lead to flash, which results in wasted material that must be trimmed and discarded.
By improving mold design, manufacturers can significantly cut down on wasted plastic while maintaining part quality.
How Can Processing Parameters Be Adjusted to Reduce Waste?
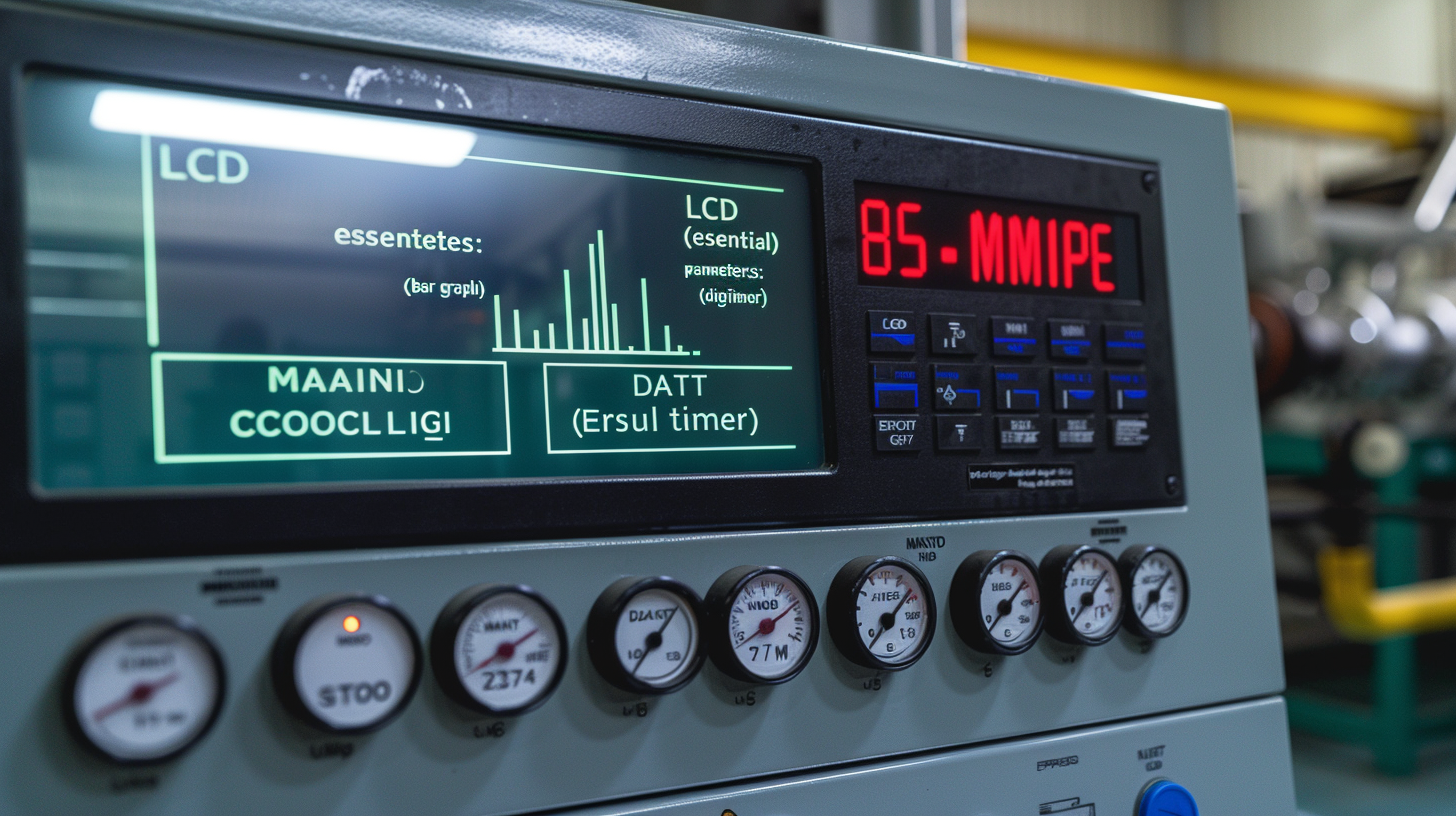
Optimizing process parameters like injection speed, pressure, and cooling time prevents unnecessary material waste. Fine-tuning these variables ensures that only the required amount of material is used in each cycle.
Key process adjustments to minimize waste:
Optimize Injection Pressure: Too much pressure forces excess material into the mold, leading to flash and waste.
Fine-Tune Cooling Time: Reducing cooling time without affecting part quality helps improve efficiency while preventing defects.
Use Scientific Molding Techniques: Data-driven molding strategies help reduce inconsistencies and minimize the need for rework and scrap.
Why Is Recycling Excess Material Important?
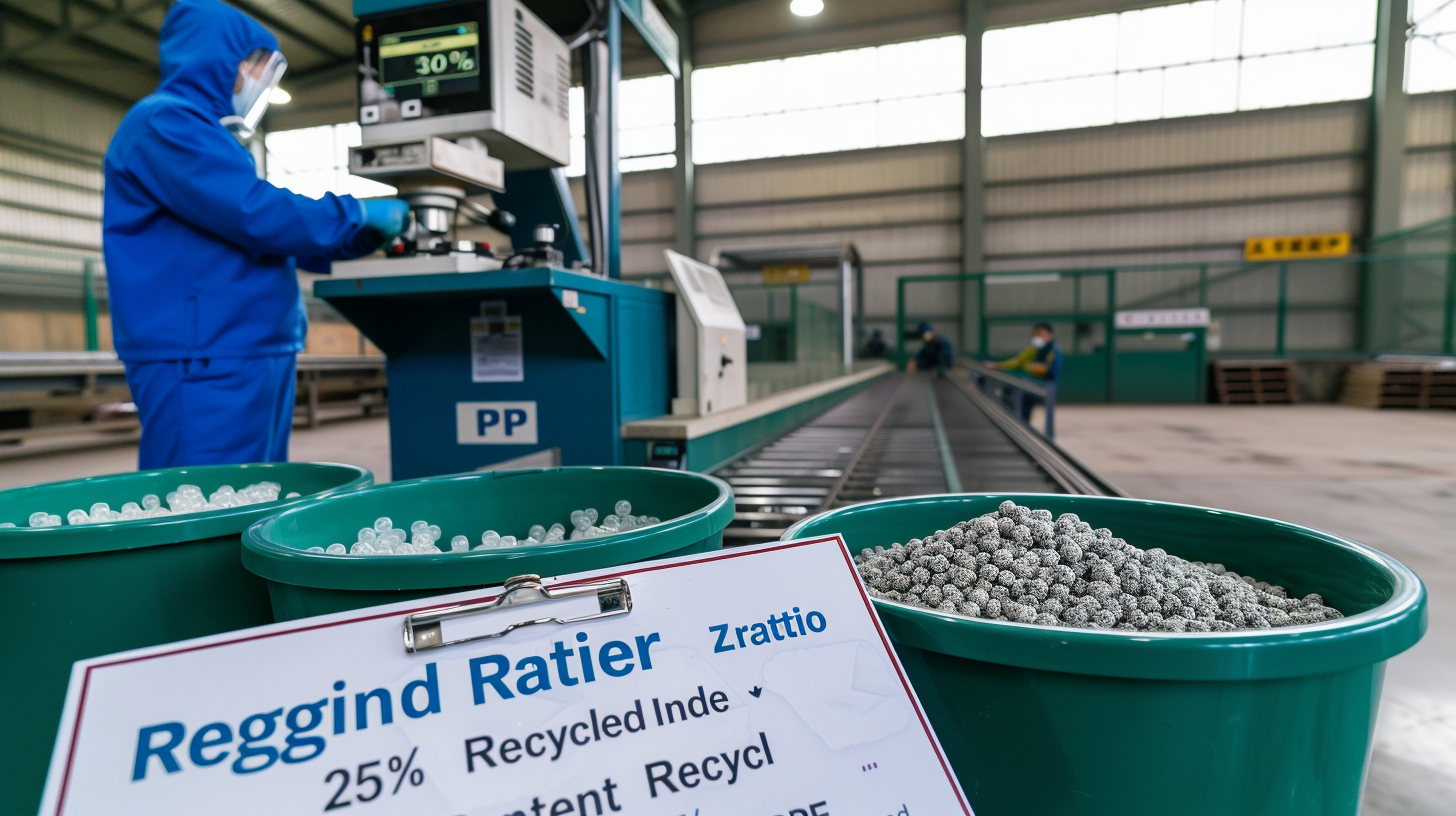
Recycling scrap material is one of the most effective ways to reduce waste in injection molding. Regrinding and reusing excess plastic can lower costs while maintaining sustainability.
Recycling strategies in injection molding:
Regrind and Reuse Sprues and Runners: Reprocessing leftover material for future use significantly reduces overall waste.
Use Recycled Resins: Many high-quality recycled plastics can be incorporated into new production runs without compromising part performance.
Implement Closed-Loop Recycling Systems: Collecting and reprocessing waste materials on-site ensures minimal loss.
Manufacturers who integrate recycling practices into their operations can achieve both cost savings and environmental benefits.
Comparison of Waste Reduction Strategies
Strategy | Impact on Waste Reduction | Best Practice |
Optimized Mold Design | Minimizes scrap and improves efficiency | Use hot runners, optimize gate placement |
Process Optimization | Prevents overuse of material | Adjust injection pressure and cooling |
Recycling & Reuse | Reduces environmental impact and costs | Implement regrind systems and closed-loop recycling |
Key Tips for Reducing Material Waste
Improve Mold Efficiency: Design molds that minimize excess material, reducing the need for secondary trimming.
Monitor Process Parameters: Regularly adjust settings like pressure and cooling time to optimize efficiency.
Recycle Excess Plastic: Use regrind systems to repurpose leftover material into new production cycles.
Use Advanced Software: Mold flow analysis tools help predict and minimize material waste before production begins.
Conclusion
Reducing material waste in injection molding requires a combination of efficient mold design, optimized processing parameters, and sustainable recycling practices. By implementing these best practices, manufacturers can enhance efficiency, reduce costs, and promote sustainability in production.
For expert guidance on optimizing your injection molding process and minimizing waste, visit our resource center or contact us. Let’s work together to create high-quality, sustainable molded parts!
Post time: Feb-18-2025